FPT Industrial a déployé sur son site de Bourbon-Lancy une flotte de six robots mobiles autonomes. Les AMR (Autonomous Mobile Robots) de Sherpa Mobile Robotics, qui automatisent les flux intra-logistiques, effectuent leur mission parmi les opérateurs, les AGV, les chariots de manutention et autres équipements de production déployés dans l’atelier. La ligne d’assemblage des moteurs, qui opère en deux équipes les jours ouvrés, a été réorganisée pour tirer profit de cette flotte de six robots gérée par son logiciel Fleet Management System.
L’usine FPT Industrial de Bourbon-Lancy (Saône-et-Loire) assemble 35 000 moteurs par an. Ces moteurs sont destinés à équiper des machines agricoles, des bus et aux autres camions. Il s’agit de pièces lourdes et volumineuses dont le montage réclame des outillages spécifiques. Ces équipements occupent un volume important au bord des lignes d’assemblage. « Nous souhaitions améliorer le flux logistique et les conditions de travail de nos opérateurs », explique Malaurie Faivre, responsable Ingénierie logistique et Environnement chez FPT Industrial. Pour ce faire, l’entreprise a déployé une flotte de robots mobiles et collaboratifs de Sherpa Mobile Robotics dont les missions peuvent, contrairement aux véhicules guidés automatiquement tels que les AGV (Automated Guided Vehicle), plus facilement être configurées et modifiés. Les robots mobiles autonomes AMR (Autonomous Mobile Robots) ne sont pas déployés sur un seul parcours et focalisés sur une unique mission. Leurs déplacements sont programmables au gré des exigences, des nécessités, de l’environnement et des contraintes industriels.
Approvisionnement en juste à temps
L’assemblage des 150 moteurs quotidiennement s’effectue sur deux lignes parallèles séparées par une allée centrale : l’une est dédiée à la préparation des sous éléments, l’autre au montage. Les six robots opèrent par couple pour chacun des trois postes d’assemblage (supports moteur, volants moteur et bassins). Chaque robot transporte un sous ensemble préparé et monté de la zone de préparation à celle d’assemblage puis en revient. Un opérateur est chargé de la préparation des composants, alors qu’un autre se charge de la réception sur la ligne d’assemblage. Ainsi, l’opérateur ne quitte pas sa zone de travail. Les robots mobiles l’approvisionnent en pièces et en outillage dont il a besoin. « Le robot arrive donc au bon moment avec les bonnes pièces », souligne Damien Winling, directeur technique chez Sherpa Mobile Robotics. Celles-ci sont préparées et disposées de façon à être prêtes à l’assemblage sur la ligne dédiée à ces opérations. Ce mode d’approvisionnement en juste temps permet de gagner en fluidité et en productivité tout en réduisant la pénibilité des tâches et les risques lors du transport des charges. « En augmentant notre productivité et en tendant vers le One Piece Flow, ces robots s’inscrivent pleinement dans notre démarche 4.0 », observe Malaurie Faivre.
Durant leur 20 heures d’utilisation quotidienne, les robots effectuent 450 missions. « Les opérateurs les ont facilement acceptés du fait de leur facilité d’utilisation », déclare Mathilde Forat, animatrice WCM logistique chez FPT Industrial. « Grâce à leur interface intuitive, leur prise en main est aisée. De plus, en mode Follow Me, le robot peut se déplacer en interaction avec l’opérateur », rapporte Paulo Figueira, Technicien Méthode Logistique.
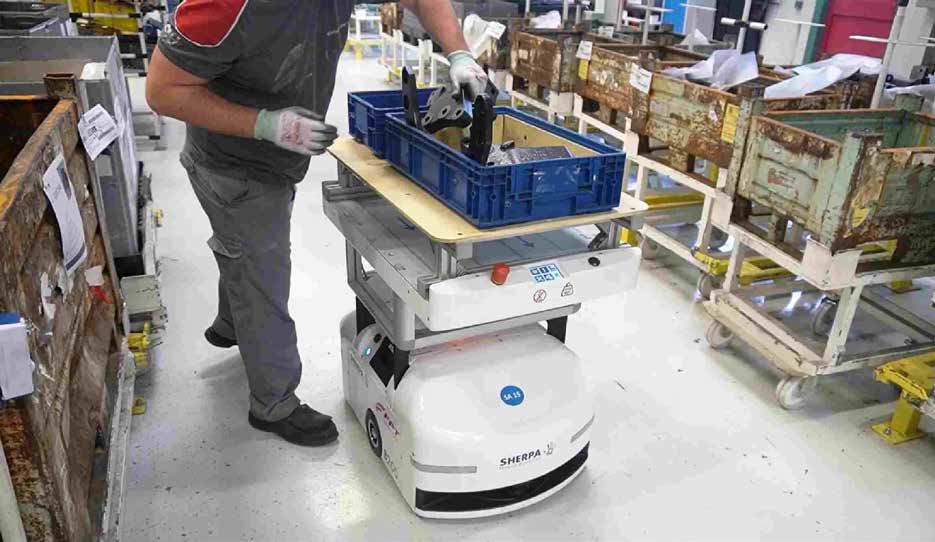
Solution de gestion de flotte
Les missions de la flotte de robots sont pilotées par le logiciel Fleet Management System (FMS) de Sherpa compatibles avec tous les robots du constructeur. Le déploiement des robots et du logiciel de gestion ne nécessite pas de modification d’infrastructure, ni du système informatique. Le FMS propose une vue cartographiée de la zone de travail représentant les déplacements de chaque robot, avec des indicateurs de missions (heure, déplacement, charge, etc.) et l’état de leurs batteries. Elle communique avec chaque robot dont la mission a été préalablement définie. La fin de chaque mission ou de la préparation lui est signalée par l’opérateur via l’IHM du robot. Le FMS gère la séquence des robots, et peut les mettre en attente dans une zone dédiée. FPT Industrial a la possibilité de changer les configurations et les missions de ses robots. Le FMS fonctionne en alternance avec le mode Follow me (suiveur) : lorsque le robot se trouve dans la zone d’assemblage, il passe en mode Follow me et suit les déplacements de l’opérateur grâce aux capteurs embarqués.
Le robot collaboratif se charge des pièces lourdes
FPT Industrial explore le potentiel des robots collaboratifs dans son usine de Turin, dédiée à la production de transmissions et d’essieux pour les engins de chantier, les machines agricoles et les poids lourds.
Le robot AURA (Advanced Use Robotic Arm), conçu par Comau, est déployé dans le département dédié à l’assemblage des broches pour les essieux des équipements lourds. Malgré ses trois mètres de hauteur et son poids d’environ trois tonnes, ce robot industriel collaboratif peut travailler aux côtés d’opérateurs avec qui il partage le même espace de travail sans nécessiter de barrières de protection. Il peut, en cas de besoin et dans certaines situations, être guidé manuellement par l’opérateur qu’il aide à effectuer les tâches les plus fatigantes et répétitives. « Cette application robotisée collaborative mise en œuvre à l’usine de Turin Driveline est une avancée importante. Le robot améliore l’ergonomie des opérations d’assemblage manuel des pièces lourdes », souligne Giuseppe Daresta, responsable de la fabrication chez FPT Industrial.
Le robot récupère une pièce sur un chariot d’approvisionnement pour la mettre à disposition de l’opérateur avec lequel il partage le poste de travail. L’opérateur prend ensuite le contrôle des opérations en guidant le robot par une poignée afin que le bras poly-articulé dépose la pièce sur un établi. Le robot prend en charge la manipulation de pièces lourdes pesant jusqu’à 170 kilos, tandis que les tâches d’assemblage sont effectuées par l’opérateur qui adapte ses interventions à la diversité des procédures et des stratégies d’assemblage qui varient fortement d’une pièce à l’autre.
Le robot intègre des dispositifs de détection lui permettant de percevoir toute présence dans son champ d’action, qu’il s’agisse d’un équipement mobile ou d’un individu. Il adapte son fonctionnement en conséquence. Sa ‘’peau sensible’’ lui permet de repérer toute présence à proximité et de réduire sa vitesse ou s’arrêter complètement pour éviter toute collision. Sa caméra 3D lui permet de déterminer la position de la pièce à déplacer avant de la saisir avec sa pince. Un scrutateur laser surveille en outre toute intrusion dans son espace de travail lorsqu’il est en mouvement. Le robot peut donc travailler sans barrières en toute sécurité au côté d’un opérateur sur la chaîne d’assemblage des systèmes de transmission.
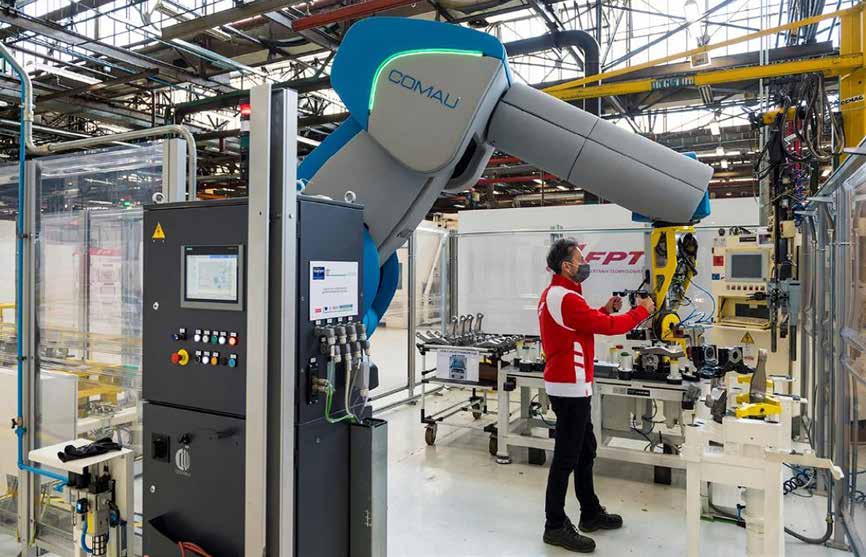
Déplacements autonomes et sécurisés
Les robots mobiles évoluent dans l’usine en présence des opérateurs, des chariots et des AGV. Ils ne sont pas guidés par des dispositifs laser ni ou autres repères au sol mais par un système de géolocalisation embarqué s’appuyant sur la cartographie de l’espace et de routes prédéfinies. Avec leur électronique de sécurité et leur lidar qui sonde leur environnement sur 360°, associé à des capteurs et des bordures sensibles, ils repèrent les obstacles ou les personne se trouvant sur leur passage. Afin de permettre la circulation des robots parmi le flux des AGV déjà en place sur le site, Sherpa a développé un système de barrage mettant en œuvre des portes virtuelles. Ces portes s’ouvrent ou se ferment en fonction de la circulation des AGV. Lorsque un AGV se présente, une porte virtuelle arrête le robot puis la porte s’ouvre pour lui signaler qu’il peut poursuivre son trajet.