Depuis l’avènement des technologies brushless il y a une vingtaine d’années, les solutions de contrôle de mouvements ont atteint leur maturité sur le plan des performances. Désormais, beaucoup de fabricants de machines et d’entreprises du secteur manufacturier donnent la priorité à d’autres objectifs. La réduction de la consommation d’énergie en fait partie. Selon Wilfried Guerry, chef de produit Motion Control chez B&R, la conception même des moteurs et des variateurs impacte directement l’efficacité énergétique des machines. À tel point que les nouveaux enjeux énergétiques justifient aujourd’hui le développement de nouvelles fonctionnalités avancées voire de nouvelles conceptions matérielles.
La hausse des coûts de l’énergie atteint des sommets. Or, d’après les retours client dont dispose B&R, les moteurs électriques et les dispositifs qui les contrôlent arrivent au troisième rang des postes qui consomment le plus d’énergie dans les machines, après les fours et les compresseurs d’air. La consommation d’énergie électrique des machines dépend bien sûr de nombreux facteurs propres à chaque application. Parmi les phénomènes causant des pertes électriques importantes, il en existe qui sont communs à la plupart des applications existantes comme l’énergie réactive et les pertes liées aux moteurs ou à la vitesse de commutation des transistors de puissance.
L’énergie réactive, non convertible en énergie mécanique, représente plus de 15 % du coût de la consommation d’énergie électrique. Des solutions de correction de facteur de puissance (PFC) dites « actives » annulent quasiment cette composante réactive de l’énergie consommée tout en réinjectant le surplus d’énergie de freinage sur le réseau électrique. B&R les propose depuis plus de quinze ans dans ses servovariateurs ACOPOSmulti. Les utilisateurs disposant d’une solution passive (avec CFC seule) avec ces servovariateurs peuvent passer à une solution active et réduire ainsi la facture d’électricité via un simple échange du module d’alimentation.
La conception du moteur a également un impact important sur la consommation d’électricité. À taille identique, les moteurs à haute densité d’énergie que proposent certains constructeurs comme B&R délivrent près de 50 % de couple en plus par rapport aux moteurs standard. Ce gain d’efficacité, qui permet de fournir la même puissance mécanique tout en consommant moins d’électricité, est aujourd’hui attesté par le China Energy Label (CEL), une certification désormais obligatoire pour la vente de servomoteurs en Chine. Le système d’entraînement B&R résultant de l’association d’un moteur à haute densité et d’un servovariateur ACOPOS est certifié CEL Class 1.
Cartographie de la consommation électrique
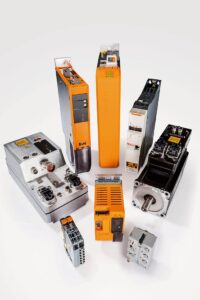
Pour aller plus loin dans la maîtrise de la consommation électrique des servovariateurs dans les machines, il faut également disposer d’une cartographie complète de la consommation électrique de la machine, autrement dit savoir ce que consomme chaque servovariateur et à quel moment dans le cycle machine. Des solutions existent pour surveiller la consommation électrique des machines. Néanmoins, elles ne permettent pas de connaître la consommation de chaque servovariateur, ni à quel moment les pics de consommation des servovariateurs se produisent dans le cycle machine. Le repère temporel dans le cycle machine est perdu. Pour remédier à cela, B&R intégrera cette année une fonction de monitoring énergétique dans ses servovariateurs. Cette fonction permettra de savoir exactement et à tout moment ce que consomme ou regénère chaque servovariateur dans la machine. Le profil de mouvement appliqué à chaque moteur pourra être ainsi optimisé sur un plan énergétique. En outre, les servovariateurs de B&R peuvent réduire leurs pertes électriques de 30 % lors de certaines phases d’activité en réduisant automatiquement la fréquence de fonctionnement de leurs étages de puissance. Tout cela permet d’optimiser dès à présent la consommation électrique des machines. Ces nouvelles fonctions permettront également de proposer, dans un avenir proche, des fonctions de maintenance prédictive et prescriptive. En effet, un changement inattendu de la consommation d’électricité d’une machine peut révéler un problème mécanique naissant et donc la nécessité d’une action de maintenance.
Pilotage de l’électronique de commande
Toutes ces mesures, aussi efficaces soient-elles, ne permettent pas d’assurer une efficacité énergétique maximale en toutes circonstances. À cet effet, il est nécessaire d’introduire une rupture technologique au niveau des étages de puissance. B&R a fait le choix de développer une solution hybride alliant les avantages des technologies IGBT et MOSFET grâce à un arrangement très particulier de ces éléments et à une technique brevetée de pilotage de l’électronique de commande. Cette solution, qui a déjà été testée avec succès en laboratoire et sur des machines chez des clients pilotes, permet d’atteindre une efficacité énergétique proche de 99 % pour une puissance nominale délivrée de 32 kW. Étant par défaut « active », elle intègre aussi les éléments nécessaires pour la correction du facteur de puissance et la réinjection réseau. Toutes ces caractéristiques permettent son utilisation sans filtre CEM additionnel ni self de régénération. Ainsi, elle nécessite environ 68 % d’espace en moins par rapport à la solution « active » aujourd’hui disponible. La nouvelle technologie permet également de réduire de manière très importante les courants de fuite nécessitant souvent l’ajout de disjoncteurs différentiels de 300 mA coûteux ou de transformateurs d’isolement.