L’industrie 4.0 promet de
remodeler l’usine à grand renfort
de technologies numériques. Reste
qu’une stratégie pérenne implique
d’engager la transformation là où
elle maximise les gains financiers,
les économies de temps et
simplifie les processus pour les
opérateurs tout en réduisant la
pénibilité. Quelques experts de la
transformation digitale partagent
avec nous leur expérience et…
leurs espoirs.
Entre les technologies de la troisième révolution industrielle qui a vu les robots et les systèmes automatisés pénétrer les usines et la transformation aujourd’hui à l’œuvre, la principale différence réside dans l’introduction de l’interopérabilité et de la connectivité entre les équipements industriels, les automates, les systèmes de supervision de la production et l’informatique des entreprises.
Au fur et à mesure que la technologie évoluera et que son adoption s’étendra, les entreprises devraient atteindre une efficacité et une productivité accrues, économisant du temps et de l’argent en diminuant notamment la consommation d’énergie pour mieux soutenir la croissance mondiale.
Pourtant, les premières les premières tentatives de vente du concept aux entreprises n’ont pas nécessairement convaincu. « Au départ, l’Industrie 4.0 était perçue comme une notion essentiellement marketing née en Allemagne et qui ne semblait pas destinées à dépasser ses frontières », explique Steve Sands, directeur de la gestion des produits et du marketing chez Festo. « Je pense que le concept a même été dévoyé par certaines entreprises qui se sont contentées d’ajouter un sticker sur leurs machines pour affirmer qu’il s’agissait d’industrie 4.0. » « Au lieu d’aborder l’Industrie 4.0 comme un moyen de transformer l’ensemble de la production, une approche plus réaliste consiste à se concentrer sur des objectifs bien circonscrits et rapidement atteignables », soutient Martin Walder, vice-président de l’automatisation industrielle chez Schneider Electric. « Je recommande d’aborder la transformation numérique par étapes, en laissant aux personnels le temps de se familiariser avec le changement puis d’accélérer les déploiements lorsque chacun se sent à l’aise. »
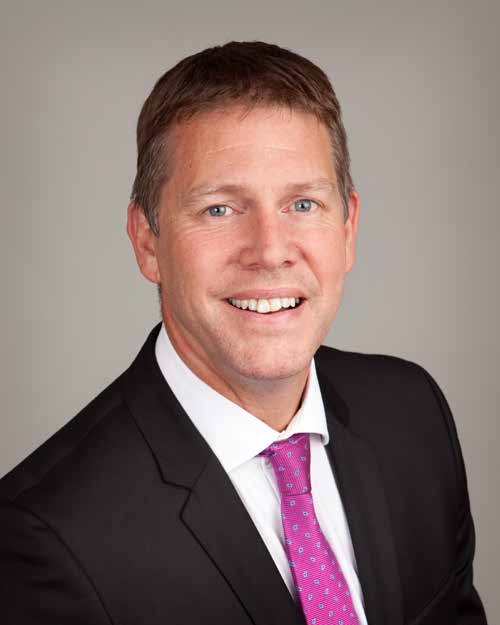
Steve Sands considère la maintenance prédictive comme un véritable débouché pour l’Industrie 4.0 car son retour sur investissement est facile à mesurer. Pour tous les fabricants dans le monde, les temps d’arrêt dus à des pannes de machines ainsi que la maintenance planifiée de manière rigide constituent un important poste de dépense. En équipant les machines-outils et les cellules de production avec des capteurs et en utilisant parfois conjointement, des logiciels installés localement ou exécutés depuis le cloud pour surveiller les conditions de fonctionnement, il est possible de détecter des signaux indiquant une usure susceptible de provoquer une défaillance à court terme. Les techniciens peuvent dès lors intervenir lorsque c’est nécessaire plutôt qu’en se conformant aux principes d’un calendrier immuable. C’est ce que Jeff Barnes, directeur des comptes d’entreprise pour Molex en Europe, explique en notant que : « avec la maintenance prédictive, un constructeur de machines peut prédire un problème et n’envoyer des intervenants que lorsqu’une réparation s’impose. »
Surtout, l’anticipation des incidents permet de planifier les réparations aux périodes les plus favorables à la productivité au lieu de se voir contraint de réagir à une panne dans l’urgence, le plus souvent dans une période de pointe sur la ligne de production impactée. L’opérateur peut planifier la maintenance lorsque la machine-outil, la cellule ou le robot concerné sera moins intensément utilisé et que d’autres équipements pourront être mobilisés pour récupérer sa charge de travail. « Nous pouvons promouvoir l’industrie 4.0 auprès des fabricants de machines dans ces domaines d’applications et leur garantir tant une productivité accrue qu’une connaissance approfondie de leurs propres équipements, ce qui offre de bien meilleures opportunités », insiste Steve Sands.
LE DÉFI DU DÉVELOPPEMENT DURABLE
D’autres paramètres tels que l’efficacité énergétique, apportent un éclairage nouveau sur les coûts, de production que les constructeurs de systèmes industriels n’ont pas nécessairement intégrés par le passé et qui conduisent vers une profonde transformation de l’industrie mondiale sur le long terme.
« L’automatisation d’une usine entraîne des coûts importants et les industriels sont – à juste raison – souvent conservateurs. Ils savent ce qui fonctionnent et n’ignorent pas que changer leurs pratiques ne va pas sans risque.
Ainsi, les équipes chargées du fonctionnement de l’usine seront réticentes à adopter des pratiques pour lesquelles elles n’ont que peu ou pas d’expérience », tient à rappeler Martin Walder de Schneider Electric. « L’industrie 4.0 ne concerne pas seulement les personnes qui la mettent en œuvre. Elle impacte directement celles qui l’opèrent et travaillent avec elle au quotidien. Il est impératif d’emporter l’adhésion de ces acteurs et de s’attacher à parler la même langue que les opérateurs. »
Un autre problème est celui des compétences qui sont déjà nécessaires aujourd’hui et le seront plus encore demain, pour implémenter l’Industrie 4.0 dans large éventail d’applications. « Les PME n’ont parfois pas d’ingénieur spécialisé dans les questions d’intégration de la connectivité en milieu industriel qui s’appuie sur des protocoles spécifiques pour l’automatisation, la sécurité des personnes et des installations, etc.
Contrairement aux révolutions industrielles précédentes, l’Industrie 4.0 implique de faire collaborer des services qui n’avaient auparavant jamais étroitement travaillé ensemble. Par exemple, les services informatiques (IT) sont depuis toujours mobilisés sur la gestion au sens large (comptabilité, action commerciale, paie, ressources humaines, bureautique, gestion documentaire, etc.) tandis que les ingénieurs et techniciens en automatisation et informatique industrielle (OT) gèrent les équipements et les logiciels destinés au séquençage, au pilotage et à la surveillance des machines de production.
Les développements qui s’inscrivent dans le sillage de l’Industrie 4.0, tendent à faire converger ces deux espaces de ressources numériques pour, à terme, exploiter un flux de données qui va de la prise de commande à la planification de la production en passant par la logistique et la relation-client. Pour cela, les technologies de l’information et les technologies opérationnelles doivent impérativement parler la même langue.
« On peut difficilement mettre en œuvre une solution Industrie 4.0 sans que le service informatique soit totalement impliqué dans le projet. Il faut constituer de véritables équipes transverses, capables d’intervenir partout dans les entreprises. Il faut par exemple, que des personnes possèdent des compétences combinées en science des données et en sécurité informatique alors que rares sont les écoles et les universités qui forment d’ores et déjà leurs étudiants pour qu’ils maîtrisent ces différents domaines technologiques », constate Steve Sands de Festo.
Les fournisseurs ont un rôle à jouer pour aider les utilisateurs à déployer les technologies. Thomas Dale, directeur de l’ingénierie chez Omega, souligne que : « la facilité d’utilisation et la facilité d’installation favoriseront l’adoption et l’acceptation. »
« Dans les grandes entreprises, il serait intéressant qu’un manager de la stratégie Industrie 4.0 supervise et fasse le lien entre toutes les activités qui relève de près ou de loin de la connectivité des objets industriels (IIoT) », déclare Sara Ghaemi, Key Account Management Team Leader chez Panasonic Automotive and Industrial Systems en Europe.
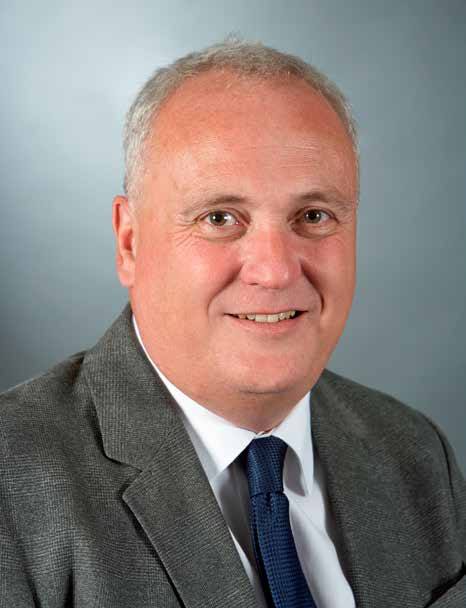
En plus de la pénurie de compétences, on constate des préoccupations croissantes concernant les réseaux non sécurisés lors de la mise en œuvre des technologies de l’Industrie 4.0. Les problèmes de cybersécurité constituent un frein puissant au déploiement de systèmes d’interconnexion IT – OT, tant les risques sont à la fois nombreux et inquiétants. Il y a ceux qui pèsent sur les machines comme la prise de commande à distance ou la corruption de leurs paramètres de fonctionnement par un programme malveillant. Il y a aussi de manière plus générale, le vol des données stratégiques, l’espionnage des processus, le détournement de brevets ou encore, le pillage ou la destruction des informations hébergées dans le cloud. Sara Ghaemi souligne que : « Panasonic travaille déjà avec des partenaires pour intégrer les normes de sécurité les plus élevées dans ses produits. ».